Superior Dental Prosthetics with Integrated Sintering Furnaces
Superior Dental Prosthetics with Integrated Sintering Furnaces
Blog Article
The world of dentistry has actually experienced a cutting edge change over the last couple of decades, with dental CAD/CAM (computer-aided design/computer-aided production) modern technology at the leading edge of this advancement. This high-tech development uses sophisticated software and exact equipment to layout and manufacture dental restorations, such as crowns, bridges, inlays, veneers, and onlays. Dental CAD/CAM milling burs are a crucial component in this process, playing an essential role in shaping complex dental remediations with remarkable accuracy.
Milling burs are reducing devices utilized along with dental milling devices to take and end up dental prosthetics from different materials. These devices need to be very resilient and sharp, provided the accuracy called for and the firmness of products they usually deal with. Common products consist of resins, ceramics, and steels, although significantly, zirconia has come to be the material of choice for lots of dental restorations because of its remarkable strength, biocompatibility, and aesthetic possibility.
Dental zirconia blanks, occasionally referred to as zirconia discs or blocks, are pre-manufactured types of zirconia used in the milling procedure. The production of dental zirconia starts with the formation of these spaces.
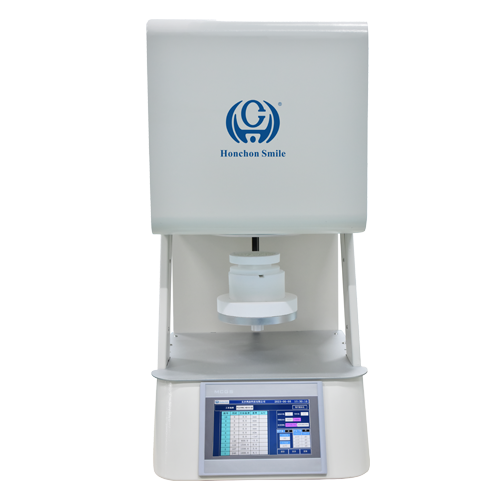
Check out the current advancements in dental CAD/CAM technology, zirconia milling, and 5-axis dental milling makers that are transforming restorative dentistry. Discover how advancements like zirconia sintering furnace are boosting individual, precision, and effectiveness complete satisfaction in modern-day dental care.
When the zirconia blanks are formed, they need to be sintered, generally in a zirconia sintering furnace. Sintering is a thermal procedure designed to create a strong mass from powder without melting it. During sintering, the zirconia fragments fuse together at high temperatures, enhancing the material's density and mechanical buildings while achieving the desired clarity and shade slopes. A zirconia sintering furnace is a customized item of equipment with the ability of achieving the heats needed for this process, commonly in the variety of 1350 ° C to 1600 ° C. The sintering procedure is important, as it supports the zirconia structure and locks in its aesthetic and biocompatible high qualities.
Advanced milling makers, particularly 5-axis dental milling equipments, have actually reinvented the production of dental remediations. Generally, dental remediations required labor-intensive processes and a significant amount of time to create. The development to 5-axis innovation has transformed this considerably. Unlike 3-axis devices, which move in 3 linear axes (X, z, and y), 5-axis makers add two added rotational axes (A and B). This gives the milling machine the versatility to approach the zirconia blank from any type of angle, which is seriously vital for developing intricate forms and damages properly and successfully. The outcome is precision-crafted reconstructions that fit far better, really feel a lot more comfortable, and look more natural.
Furthermore, current years have seen the intro of 3D plus Multilayer Blocks. These cutting-edge materials integrate the advantages of multi-layered zirconia with the precision of 3D printing innovation. The multi-layered element describes the gradient in color and translucency within the zirconia block, simulating the all-natural change from dentin to enamel found in real teeth. This gradient impact is accomplished by layering various tones and levels of clarity of zirconia within the block throughout production. Subsequently, when this multi-layered block is grated, the resulting repair looks much more realistic and needs very little post-processing or discoloring to match the client's natural teeth.
3D printing technology has actually added one more layer of customization and precision to this strategy. By integrating CAD/CAM layouts with 3D printing, the intricate details of the dental reconstruction can be captured and published layer by layer. This brings about even higher precision in fit and visual appeals, which is extremely important for person complete satisfaction.
The combination of dental CAD/CAM systems, top notch milling burs, dental zirconia blanks, innovative sintering furnaces, 5-axis milling devices, and the most recent innovation in 3D plus Multilayer Blocks exemplifies the future of dental prosthetics. Dental professionals can supply far better solution with quicker turn-around times, while people profit from even more sturdy, better-fitting, and cosmetically pleasing restorations.
For example, the precision managed by these modern technologies suggests prosthetics can be created and produced with a high degree of precision, lowering the demand for duplicated changes or installations. This level of accuracy is mainly driven by the top quality of dental CAD/CAM systems and the usage of superior milling burs efficient in fine outlining. Additionally, the handling of dental zirconia blanks in zirconia sintering heaters guarantees that the end product meets the highest possible standards of toughness and biocompatibility.
The development of 5-axis dental milling devices has broadened the range of what is feasible in restorative dental care. These equipments can mill facility geometries and fine information which were not feasible prior to, leading the way for a lot more sophisticated dental services. This technological leap has actually additionally made it possible to leverage 3D plus Multilayer Blocks efficiently. These multilayer blocks offer natural-looking remediations that reproduce the rank of shade and translucency discovered in actual teeth.
In addition, the continuous advancement in zirconia products and CAD/CAM innovations bolsters a more effective and efficient dental care setting. Dentists can now achieve more predictable outcomes, minimizing chair time and improving client contentment. The comprehensive assimilation of these technologies into routine dental practice represents a seismic shift from reactive to positive dental care, where electronic perceptions, specific milling, and immediate modifications become basic method.
By decreasing material waste and enhancing the usage of sources, dental techniques can run a lot more sustainably. The global assimilation of these innovative products and makers into dental educational program makes certain that future dental professionals are skilled in the newest technological breakthroughs, promoting a culture of constant renovation and technology.
In recap, the harmony between dental CAD/CAM systems, durable milling burs, premium zirconia blanks, effective zirconia sintering furnaces, state-of-the-art 5-axis dental milling machines, and cutting edge 3D plus Multilayer Blocks is driving a new age in dentistry. This combination is transforming how dental restorations are designed, made, and implemented, causing much better results for both dental experts and patients. As modern technology remains to progress, the future holds much more pledge for advancements that will certainly even more revolutionize dental care, making it extra precise, reliable, and patient-friendly than ever in the past. Report this page